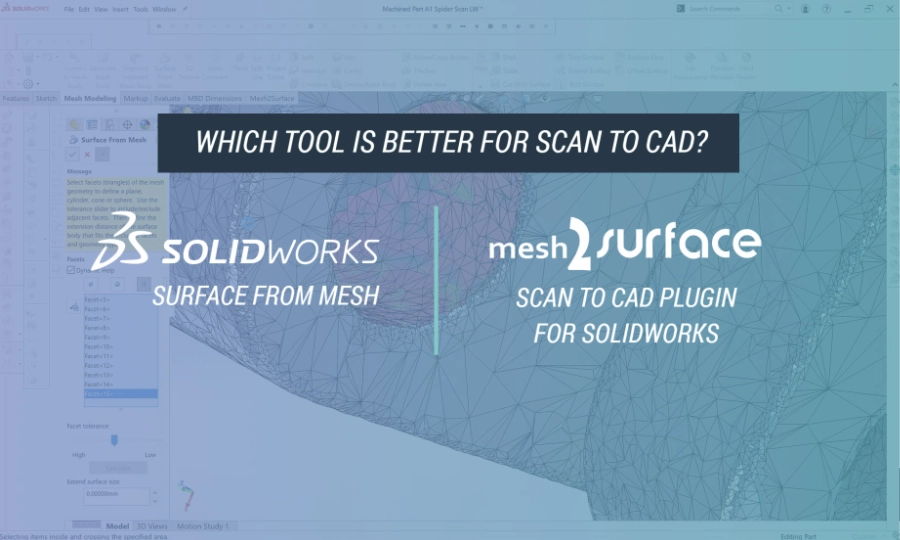
With more than 6 million designers, engineers, students, entrepreneurs, and makers using SOLIDWORKS around the world, it’s no wonder this 3D modeling software is so popular for product design and development.
There are various tools accessible inside SOLIDWORKS that can help reverse engineer a part from Scan to CAD.
What is Scan to CAD?
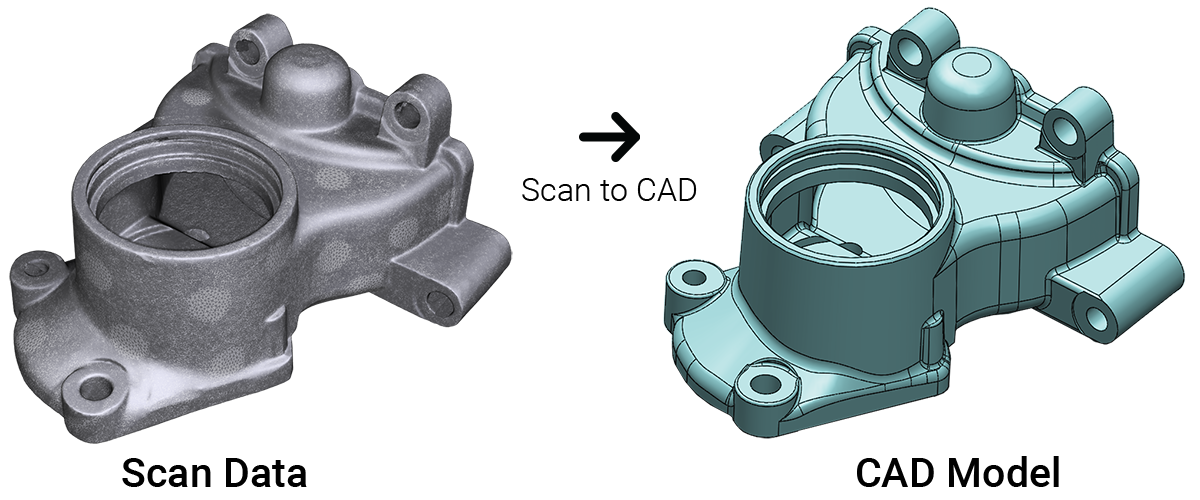
The process involves using a 3D model (captured by a 3D scanner) as a guide to constructing a CAD model. Using 3D scanner data as intel is a smarter, faster, and more accurate method of building a CAD model than doing it from a blank slate.
Using the right tool for the job can make all the difference. You can work a lot faster by using the right tool, or get frustrated by using the wrong tool because it hinders you from accomplishing your goal.
SOLIDWORKS has its own mesh modeling toolset called Surface from Mesh. The tools allow you to manipulate a mesh object that you import from an *.stl, *.obj, *.off, *.ply, *.ply2 , or *.3MF file into surfaces and solids. Typically you would export the 3D scanner data as an .stl file and import it into SOLIDWORKS to start the Scan to CAD process.
You might be wondering:
Is Surface from Mesh sufficient to do Scan to CAD projects? How do the features compare to a dedicated Scan to CAD plugin for SOLIDWORKS that’s built specifically for reverse engineering a physical product using 3D scanner data?
Let’s compare them.
Scan to CAD Projects
-
SOLIDWORKS Surface from Mesh
Toolset available in SOLIDWORKS for mesh modeling
-
Mesh2Surface plugin for SOLIDWORKS
Specialized Scan to CAD modeling toolset that works natively inside SOLIDWORKS
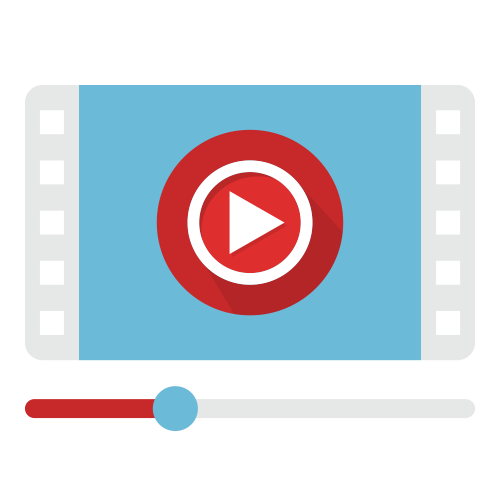
Prefer To Watch a Video Instead?
Check out the video version of this article you can watch here.
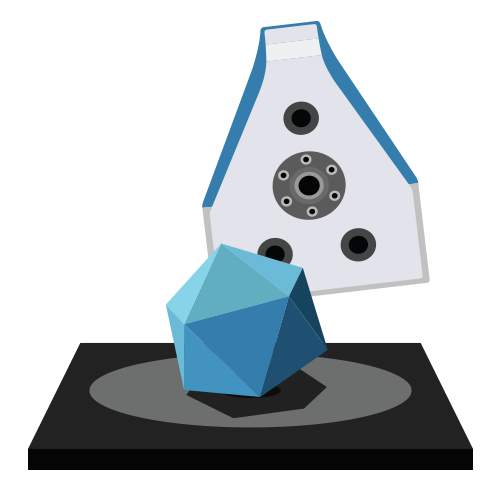
The Scan Part of the Scan to CAD Process
Our test involves capturing a 3D model of a real-world object using a 3D scanner and then importing the STL mesh inside SOLIDWORKS.
The goal: transform the 3D scan data into a parametric CAD model.
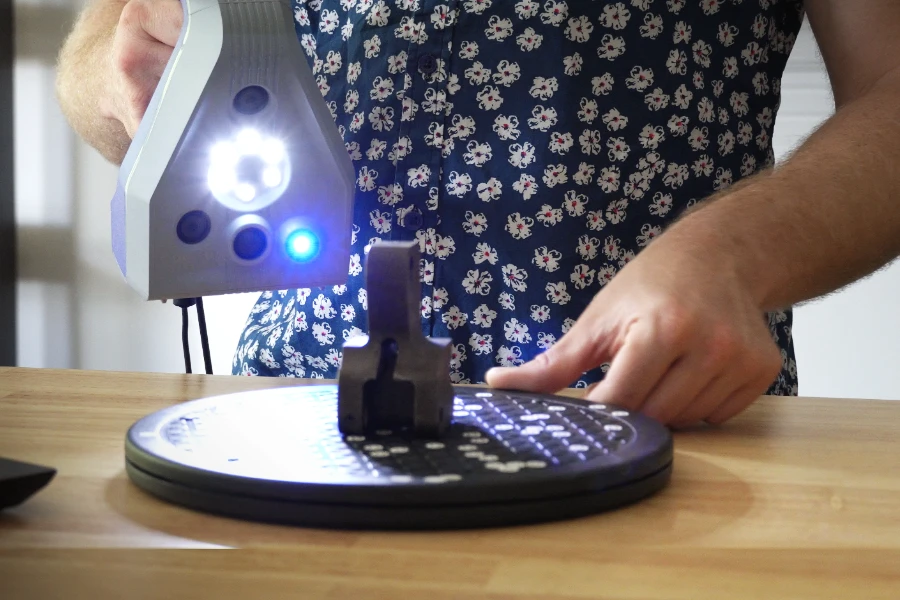
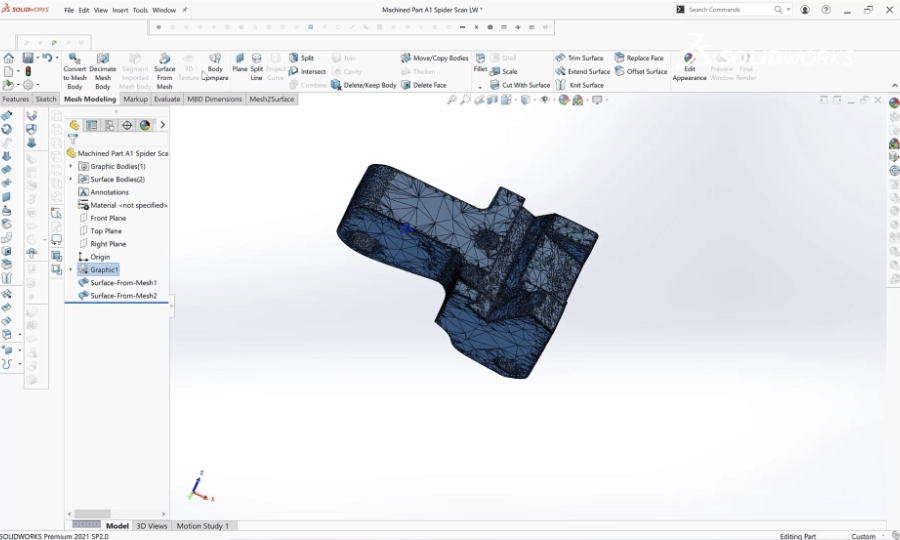
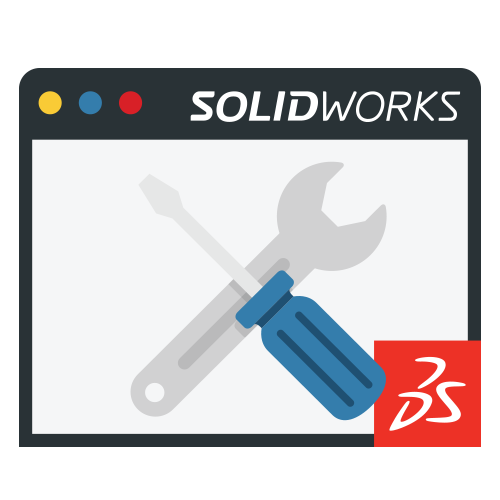
SOLIDWORKS Surface From Mesh
Here we’ll explore various aspects of the Surface from Mesh features to see how good it is at handling 3D scanner data from a professional 3D scanner.
SOLIDWORKS Surface From Mesh
-
Decimating 3D Scanner Data
Decimation is a common practice when working on Scan to CAD projects. It means reducing the number of polygons in your 3D mesh to make the file size smaller and more manageable. Using a smaller file size can speed up the Scan to CAD process as it prevents the computer from lagging if the file size is too large for your machine to handle. If done properly, you can maintain relatively good accuracy and resolution compared to the original file, without compromising on quality.
From our findings, decimating an imported 3D mesh that is 10,000 to 500,000 polygonal faces using Surface from Mesh takes approximately 20 seconds to a few minutes.
Using this 3D model as a test, it took 24 seconds to decimate the 3D model using Surface from Mesh. Mesh2Surface for SOLIDWORKS can decimate 3D scanner data almost instantaneously.
-
Creating Surfaces From 3D Scanner Data
Surface from Mesh is capable of quickly creating planes and solids (such as cylinders) from a mesh body. It works particularly well for 3D printing applications when you have to convert a mesh that was created from a pre-existing CAD file. However, the toolset has difficulties when it comes to working with 3D scanner meshes, particularly a freeform object that is not prismatic.
In our example, our machined part is prismatic but contains highly irregular meshes, which are common in 3D scanner data. Consequently, it’s difficult for Surface from Mesh to create good solids. Here, we tried to create a plane and a cylinder. -
An incomplete cylinder was created based on the 3D scanner data. -
The created plane has jagged edges all along the sides.
In line with our findings, SOLIDWORKS agrees with our results.
SOLIDWORKS Online Help states, “The tool works best on mesh files with regular prismatic geometry such as planes, cylinders, cones, and spheres. It may not be appropriate for highly irregular meshes such as those created from a 3D scan of an organic shape. Because the feature only creates surfaces, the recommended workflow is to trim the surfaces to form a solid.”
There are alternative tools such as Mesh2Surface for SOLIDWORKS that are better suited for creating solids from 3D scanner STL meshes because it’s built specifically for that purpose.
-
-
Comparing the Deviation of the Sketch to the Scan Data
The Body Compare feature allows you to see how close or how far the created surface bodies are deviating from the 3D scanner data. This is a powerful tool as it ensures the CAD model is accurate to the referenced real-world part. The visual color map makes it easy to see which areas are in and out of tolerance. You can specify the tolerance you can accept. Green means that the sketch is close to the scanned data. (It’s within the tolerance.)
Mesh2Surface for SOLIDWORKS has a powerful deviation analyzer feature as well.
Now that we looked at the Surface from Mesh toolset, let’s see how they compare with Mesh2Surface for SOLIDWORKS.
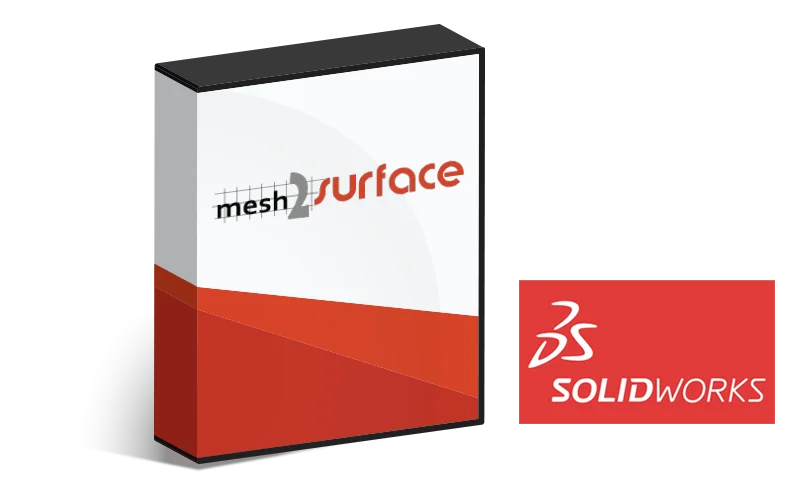
Mesh2Surface for SOLIDWORKS plugin
Once you install the Mesh2Surface plugin inside SOLIDWORKS, the Scan to CAD toolset performs as they always belong inside the 3D modeling software.
SOLIDWORKS Surface From Mesh
-
Decimating 3D Scanner Data
Using Mesh2Surface for SOLIDWORKS to decimate 3D scan data is fast and simple. If you recall, it took 24 seconds for Surface from Mesh to decimate the 3D scan data. Using the same 3D model of the scanned part, decimation took 1 second when using Mesh2Surface for SOLIDWORKS.
All you have to do is specify the decimation parameters, hit the checkmark, and the scan data is decimated in the blink of an eye. Mesh2Surface is great at handling large scan data sets. Mesh2Surface for SOLIDWORKS Decimation Test By The Numbers Number of polygon triangles (before decimation) 1,302,610 Percentage reduction of all triangles 50% Number of triangles (after decimation) 651,305 Time to decimate 1 second -
Creating Surfaces From 3D Scanner Data
Mesh2Surface was developed for Scan to CAD projects. It is equipped with intuitive tools to easily extract features from your 3D scan data or quickly reconstruct planes, cylinders, cones, and spheres. See for yourself how this process works using the SOLIDWORKS plugin.
Watch the complete walkthrough of the sketching process
Basic Workflow
-
Take a 2D cross-section of the largest section.
Mesh2Surface automatically calculates the best 2D cross-section for sketching the CAD model.
-
Sketch the 2D profile
Fit Sketch Entities tools make it quick and intuitive to create lines and geometries to sketch the outline without you redrawing it manually. It does most of the work for you.
-
Extrude or revolve the sketch into a solid body.
-
You can also do extruded cuts to subtract from solids.
-
Continue this process until you have a completed sketch of the 3D model.
Interested in exploring Mesh2Surface for SOLIDWORKS yourself?
-
-
Comparing the Deviation of the Sketch to the Scan Data
Similar to SOLIDWORKS Surface from Mesh, Mesh2Surface also has a Compare feature but with more advanced features to give you more intel to build better CAD models.
This powerful tool helps you control the accuracy and the quality of your reconstruction at a glance at any time with its color map. Set your acceptable tolerance. The deviation analyzer works with any SOLIDWORKS body (surface or solid) and compares the reference scan data with almost instant speed. Mesh2Surface for SOLIDWORKS also provides you with the percentage of points that are within the tolerance number you set. In our example below, you can see that 85.96% are within tolerance.
In this example, we set our tolerance to 0.00590551” or 0.15mm. As you can see from the color map, the sketch is mostly green which means it’s within the acceptable tolerance that we set. Our sketch is modeled closely to the 3D scan data.
Conclusion: Which Scan to CAD Tool Should I Choose?
Based on our findings, you can see that Mesh2Surface provides quicker results with better outcomes compared to Surface from Mesh. This is not surprising, as Mesh2Surface is a plugin developed for Scan to CAD projects that involve using of 3D mesh from any 3D scanner imported into SOLIDWORKS to rebuild a CAD model.
Surface to Mesh is best for 3D printing applications, or for Scan to CAD projects where the 3D mesh:
- doesn’t have irregularities, or
- is a basic prismatic part that doesn’t have organic shapes.
Mesh2Surface for SOLIDWORKS can handle more complex Scan to CAD projects. This SOLIDWORKS plugin is an affordable Scan to CAD solution compared to other solutions in the market. You can learn more about the plugin on our website. Mesh2Surface is also available for Rhino. If you are looking for a standalone Scan to CAD software, be sure to check out QuickSurface which has similar toolsets created by the same developer.