Sculptor uses 3D scanning to enhance his craft
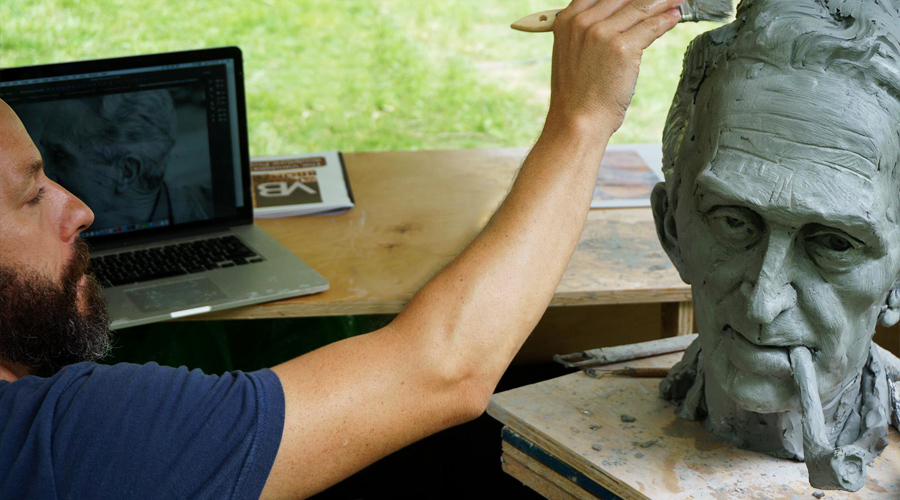
Jamie Lester, founder of Vandalia Bronze, is masterful in bringing bronze monuments to life. From his larger than life size bronze statue of NBA legend Jerry West to the Brooklyn Wall of Remembrance to commemorate the firefighters who lost their lives on 9/11, his passion for creating portraitures and figurative sculptures spans more than 20 years.
Jamie first models his original sculptures in clay before sending them off to the fine arts foundry to have his pieces cast in bronze. Being that his artwork is in the form of 3D, it is very fitting that 3D scanning would be an amazing tool to enhance his craft.
“For the longest time, I wanted to focus on the digital aspect of sculpting by using ZBrush as part of my creative process. It wasn’t until I was exposed to 3D scanning that it motivated and inspired me to pursue it even further,” Jamie explains.
Jamie first came in contact with 3D scanning when Vandalia Bronze outsourced the service for a specific project. Seeing the benefits and potential that the technology could offer, he decided to bring 3D scanning in-house. He first purchased the Artec Eva 3D scanner and then the Space Spider from GoMeasure3D to improve his design process.
Working from Clay to Bronze
Jamie begins the process of making a bronze sculpture by taking inspirations from photographs and by sketching conceptualized drawings. From there, he creates a miniature clay model, called a maquette, to work out the design issues in three-dimensional space on a small scale and to refine his design. With a clear vision of what the final sculpture would look like, he presents the maquette to his clients for approval.
Once the design has been approved, Jamie and his team creates the actual size version of the sculpture in clay.
Jamie’s team starts by welding steel in the exact shape of the model called the armature. It serves as the strong foundation that would hold up hundreds of pounds of wet clay which Jamie would use for sculpting.
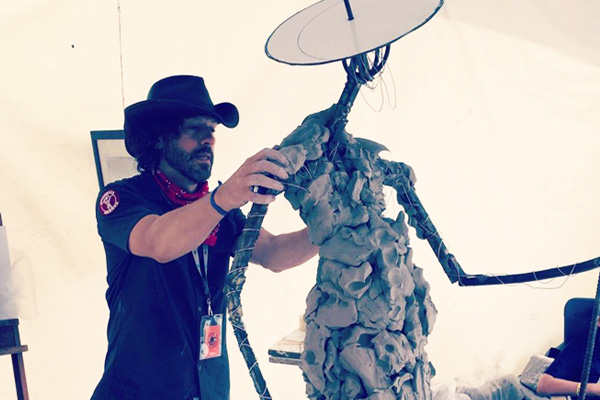
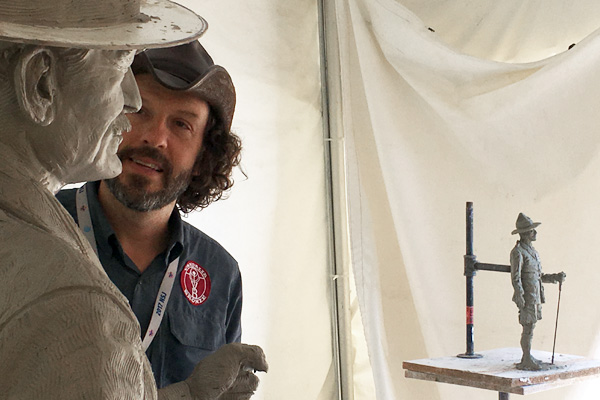
“Before, we used to make the steel skeleton frame just by eyeballing the angles and measurements. Now, we take out the guesswork by using the Artec 3D scanner to scan the maquette into a 3D digital model. We get all the measurements we need to create the full physical 3D skeleton. We can now create the steel frame faster and with better accuracy.”
With the steel frame in place, Jamie then meticulously sculpts the life size clay sculpture by hand.
“Clay plays an important part of my art because it ties the history to today. Even if I use new technology like 3D scanning, I still like to create my artwork first with a physical medium I can touch and feel with my hands.”
When the final statue is complete, he scans the model with the Artec 3D scanner once again to transform it from a physical model into a 3D digital one.
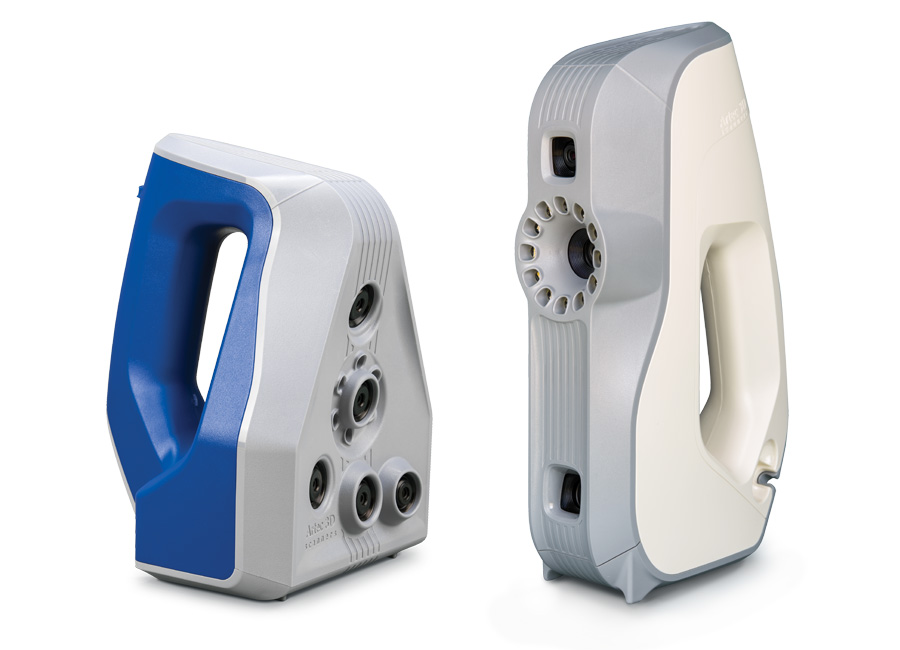
“My sculptures are about 8 feet high. The Artec Eva and Space Spider are both very good at scanning large objects. They use geometry to register scans together rather than using photogrammetry. I don’t particularly like using photogrammetry stickers because I would need to buy them regularly–which can get quite expensive–and they mark up the surface.”
A 3D scanner outputs the stl file which is then electronically sent to the foundry for bronze casting. “If I need to make modifications to my clay sculptures, previously I would have to start from scratch because I use clay. Since purchasing the scanners, I scan my sculptures digitally into 3D. I can then simply modify and do touch ups to my artwork in ZBrush before I send my final files to the foundry.”
The foundry uses the stl file to 3D print the detailed parts of the sculpture in plastic (PLA), and CNC mill foam the larger areas to recreate the sculpture back into physical form for molding. The lost wax process is used to create the final bronze sculpture.
Previously, Jamie and his team would have to create a negative rubber mold of the life size clay sculpture at the studio. Rubber is applied to the statue’s surface to create the mold. The sealant ruins the clay and prevents Jamie from reusing it again for another project. Once the rubber is cured, plaster and burlap is applied on top to create the mother mold, which will eventually be shipped to the foundry for bronze casting.
“3D scanning saves us about $2,000 in labor cost
per project by eliminating the need
to create the mold in-house.There’s no shipping cost involved and it saves us time. It’s cheaper and more convenient for us to pay the foundry to do it than doing it ourselves.”
Jamie Lester Bronze Sculptor Vandalia Bronze
“I use water clay as my medium of choice for hand sculpting. After scanning my sculptures, I can now reuse the clay after the project is complete. It’s not destroyed by the rubber sealant during the molding process if we had done it in-house.”
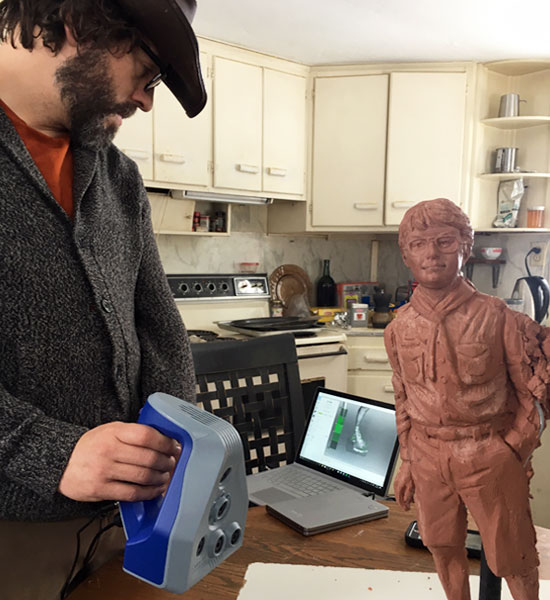
“My sculptures would eventually dry up and crack. Before, I would have no records of the handmade sculptures I put countless hours into creating. Now, I can digitally archive my work electronically on the computer using the Artec 3D scanner.”
Unlocking new potentials to 3D scanning
Jamie believes he only scratched the surface of what he can do with 3D scanning. Jamie is eager to experiment using this technology in other aspects of the project that gives his company a competitive edge.
Eventually in the early stages of his projects, he would like to scan his maquettes with the Artec 3D scanner and 3D render the outdoor environment where the bronze statues would finally be situated. He can then upload it to Sketchfab for sharing.
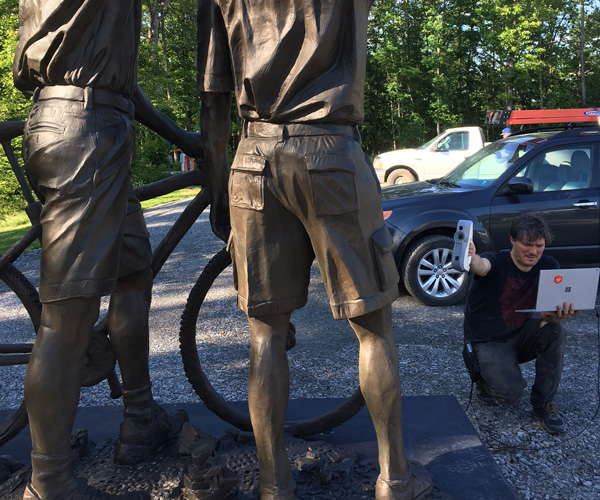
“Using photographs (2D images) to explain my proposed monuments just don’t justify how it will look in the end. My sculptures are 3D. It just seems like a logical progression to show the reviewing committee and my clients my idea in 3D since it’s more intuitive and it’s easier to understand.”
Taking it even a step further, Jamie would like to use virtual reality so people can interact with his digital sculptures from any angle in the simulated environment. This way, they have a better vision of the art piece at the outset of the project.
“3D scanner is a flexible tool that helps me view the world in a whole new way,” says Jamie. “It unleashes new creativity into the work that I’ve been doing the same way for a very long time. I’m extremely excited to integrate 3D scanning more and more into my work.”
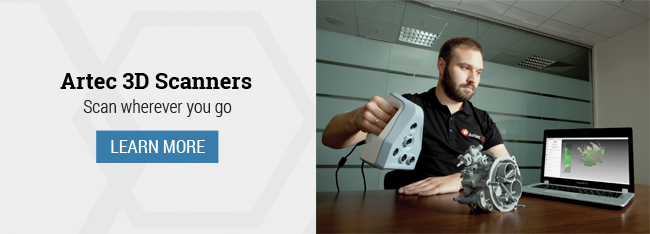
This is some really good information about using modern technology in making bronze statues. I liked that you talked about how I liked that you pointed out that using a 3D scanner can help you see how the statue looks from a lot of different angles. That would be something I would want to do before casting a statue.