We’re happy to spend some time talking with Kostadin Vrantsaliev, Product Manager of KVS Ltd. We wanted to get a better understanding of the thought process behind the development of QUICKSURFACE. It’s a new standalone reverse engineering software for converting 3D scanner data to a CAD model. We also like to know what he thinks are the trends in 3D scanning and reverse engineering.
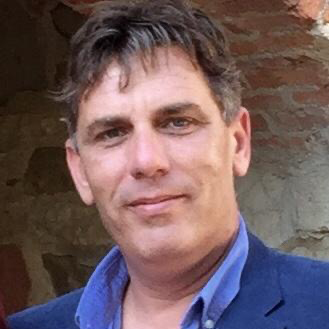
Kostadin has more than 25 years of experience in 3D scanning industry, specializing in 3D scan processing, creating 3D scan algorithms, and product design. He was a key member of the team who built the first handheld 3D laser scanner.
-
What is QUICKSURFACE in your words?
Created for professionals and non-professionals, it’s a standalone reverse engineering software for converting 3D scanned STL meshes with simplicity and ease. QUICKSURFACE is the ultimate reverse engineering solution for your 3D scanner. Instead of designing products from scratch, it provides you with an extensive toolset that makes use of 3D measurements captured from physical objects. Users can then build better and more accurate CAD models in less time than building them from scratch.
-
What was the reason behind developing QUICKSURFACE?
3D scanners have opened up in terms of affordability and accessibility, but the 3D scanning software world has yet to follow. Affordable professional-grade 3D scanners can cost substantially less than standalone mainstream reverse engineering software. I believe cost is one of the contributing factors behind why 3D scanners (hardware) are adopted by more users, while reverse engineering software is still lagging behind in its adoption.
With QUICKSURFACE, we want to shift this paradigm. At a fraction of the price, our SCAN to CAD standalone software consists of a full suite of reverse engineering tools to transform 3D scan data from any 3D scanners into usable CAD models.
QUICKSURFACE is about 1/4 of the price compared to brand name reverse engineering software. While nowadays the 3D scanning process is quite simple to perform, reconstructing a CAD model out of scans requires a lot of professional experience. We want QUICKSURFACE to be used by a wide range of users from different technical capabilities. This includes people who are not highly technical, while at the same time provide them with powerful reverse engineering tools for achieving the right results.
-
How is it that QUICKSURFACE is more affordable compared to similar standalone reverse engineering software on the market?
The way we built QUICKSURFACE was to take on a minimalist approach in designing the software. We focus on providing only the tools necessary for reverse engineering. People misunderstand reverse engineering and think it’s just about converting scan data from raw scans into a watertight mesh. Reverse engineering is much more than this. And because all the scanner manufacturers have already focused on creating meshes, we focused logically on the next steps—to create CAD models of what the real expectations are—mathematical surfaces, parametric and history representation of the scanned model.
QUICKSURFACE focuses on what it does best—reverse engineering from scan data to CAD. We’re upfront in saying it doesn’t have mesh editing tools. That’s because almost all 3D scanners already include them. This helps make QUICKSURFACE a cost-effective solution.
We are a small dedicated team that specializes in 3D reverse engineering. Compared to bigger companies that develop scan-based design software, they have larger overhead costs. We’re capable of keeping our costs down so we can pass this savings along to our customers.
-
What challenges were you looking to solve when developing QUICKSURFACE?
Anyone who has done reverse engineering before can tell you that can be a complex and time-consuming job. It’s difficult to achieve the right results while getting the accuracy you need. What we’re trying to achieve with QUICKSURFACE is to simplify the reverse engineering process. It’s about making it as efficient as possible while achieving the right results and keeping the accuracy of the CAD models with our best-fit algorithms. We’re reconstructing the reverse engineering process in a simple way without compromising on quality.
Here’s my quick video demonstration of how QUICKSURFACE works:
-
In terms of functionality, why is QUICKSURFACE different from all the other mainstream reverse engineering software that’s already out in the market?
QUICKSURFACE provides parametric hybrid modeling comprising of reconstructing both organic and prismatic shapes and merge them together into a solid or poly-surface. The software’s state of the art yet simple freeform modeling capabilities allows even non-professionals to create complex forms with ease. This method is unlike some systems that allow sketching, sectioning, and surfacing on scanned meshes.
My explanation of Parametric History-Based Modelling:
Personally, I believe QUICKSURFACE has three main advantages compared to other Scan to CAD software already out there.
Provides Real-Time Deviation Color Maps
QUICKSURFACE provides precise fitting with real-time deviation color map, allowing you to control the design intent of your work and any stage. This feature helps to identify problems early on rather than finding them at a later stage.
Controlled Automatic Surfacing
Automatic doesn’t mean you don’t have control. QUICKSURFACE has controlled automatic surfacing while other mainstream reverse engineering can’t edit as easily for this feature. With our software, you can still manually adjust the resolution and position of control points to avoid mapping the surface to the reference mesh which may have outliers and noise.
Be Productive In Less Time
Learning new software can take up a user’s time away from work. They will have to spend time on training in order to fully understand how to use it. This ultimately impacts work productivity. We built QUICKSURFACE in a way that the software’s intuitive tools and workflow would empower anyone to learn the software quickly, so you can be more productive in less time.
QUICKSURFACE provides a similar work environment to other CAD packages many users already use so it’s not like you have to learn something completely new. The streamlined user interface offers the user a quick learning curve. As a result, this is less disruptive to their daily work routine. The investment in training is minimal which allows a broad type of users to start using the software quickly.
Using QUICKSURFACE is similar to riding a bike. Even if you haven’t used it in a while, you just pick up where you left off instead of spending more time relearning the software.
-
Is QUICKSURFACE constrained by the complexity of a part?
QUICKSURFACE’s capabilities and toolsets are not limited and virtually any part can be reverse-engineered regardless of its complexity. Because QUICKSURFACE provides the power of working simultaneously with prismatic and freeform shapes, there aren’t any limitations of the solution.
The Scan to CAD software was designed for anyone who uses 3D scanning regardless of the size of the business–from individual entrepreneurs to hobbyists, small manufacturing companies to large companies who need reverse engineering. Many industries can benefit where design and 3D printing are needed including medical, dentistry, heritage, products, industrial design, automotive, aerospace, and fashion.
-
We know that you also developed Mesh2Surface. What is the difference between MESH2SURFACE and QUICKSURFACE?
Mesh2Surface is a reverse engineering plugin for Rhino CAD modeling software and QUICKSURFACE is a standalone reverse engineering software.
Rhinoceros is an affordable direct modeling CAD package. We found that it’s a great software for us to create a reverse engineering plugin for which is why we developed Mesh2Surface first. On the other hand, the other major players in the CAD industry like SOLIDWORKS, AutoCAD, and others are so-called ‘parametric modelers’. The main difference is that with a parametric modeler you can always control the parameters of the components which you use to create a model and easily apply modification in the future at any point. On the other hand, direct modelers provide a quick and straightforward way to create CAD models. The two types of users have different approaches to reconstruct CAD model and, in some cases, one or the other way of modeling is better suited for a particular job.
Both Mesh2Surface and QUICKSURFACE share a common library of tools for reverse engineering, but they cover the user experience for both types of users mentioned above. QUICKSURFACE is designed for all the people using a parametric type of modeling and thus offers the same experience as the software they are already familiar with using.
-
How are people responding to Mesh2Surface and QUICKSURFACE?
We’re very proud to receive a high user rating for Mesh2Surface on TrustPilot.
We just recently launched QUICKSURFACE. We’re very fortunate that QUICKSURFACE has received a great review by Develop3D, a highly regarded magazine which reviews essential technologies in the product development process.
-
What is the most common misconception you find people have about reverse engineering?
People assume that 3D meshes from a 3D scanner can directly become a CAD model, which is not true. A lot of times, I have to spend some time in order to give a good explanation of what and why reverse engineering is needed. 3D meshes that output from a 3D scanner lack of many properties that CAD surface do–smoothness, controllable shape, boolean operations with other shapes, the ability to create assemblies, and many more.
Let’s use an example a circle to illustrate this point. In an ideal world, a circle is perfectly round. Let’s say it’s 5mm in diameter. In the real world, all manufactured parts have some imperfections, so the circle might not be perfectly round at exactly 5mm. It can be 4.999mm or 5.1111mm. If you take a scan of the circle using a 3D scanner, the 3D mesh might capture noisy data. When reverse engineering a part to create a CAD model, you have to manually figure out that you want the circle to be 5mm and not 4.999mm or 5.111mm. There’s no magic button that can output a CAD model from a 3D scanner. It does require user involvement to figure out what is the final CAD model you want to create. This is what is known as design intention.
While there is no direct way for a 3D scanner to output as a CAD model, our main intention with the development of QUICKSURFACE, as well as Mesh2Surface, is to help people convert scan data into a CAD model as easy and as simple as possible. That’s what we’ve always set out to do from the very beginning.