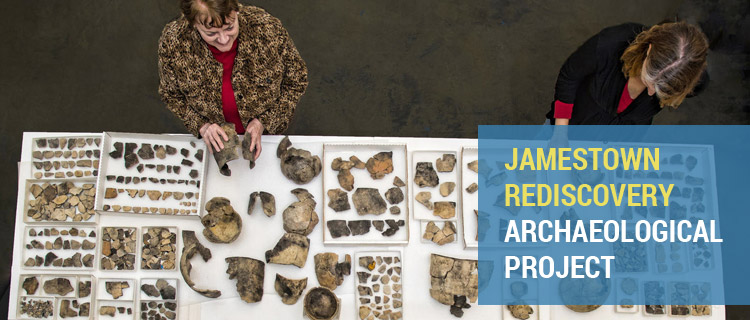
Jamestown Rediscovery is committed to the preservation, education, and the archaeological investigation of the first permanent English settlement in America more than 400 years ago. Over the past 20 years, its archaeology team found tens of thousands of Virginia Indian artifacts, including 48,000 pottery shards, at the historical site. For an upcoming exhibition devoted to Virginia’s Native Americans and their interactions with English settlers, the team wanted to connect the advancements of modern day 3D technology with history in such a way that it provided a new perspective on the James Fort period (1607–1624).
The Challenge
It’s a difficult mission to locate all the pottery shards to create a complete artifact. The archeology team at Jamestown Rediscovery wanted the public to appreciate the genuine fragments while seeing the potteries in its entirety, as they would have been originally created 400 years ago. The challenge sparked the vision to combine existing 17th-century English and Virginia Indian pottery fragments with 3D printed replicas of the missing pieces. The exhibit would display whole artifacts for public viewing in a new way. Museum visitors would be able to visually distinguish the recreated pieces from the genuine pieces to honor the past.
The Reconstruction Process
The archaeology team collaborated with GoMeasure3D and the Engineering Department at Sweet Briar College to recreate five Pocahontas-era pieces of pottery. The reconstruction process consisted of a number of powerful emerging technologies to make this project possible—from 3D scanning, 3D modeling to 3D printing. GoMeasure3D was responsible for 3D scanning the existing potteries and modeling the missing pieces digitally, while Sweet Briar College provided the 3D printing technology to recreate the newly created pieces from digital into physical form.
3D Scanning: Uncovering Clues from the Past
The archeology team at Jamestown Rediscovery assembled the incomplete pots using the original ceramic shards. The GoMeasure3D team was committed to capturing the true likeness of the pots digitally with the utmost accuracy in order to recreate the missing pieces with integrity. Non-contact 3D scanners are ideal for scanning artifacts that are delicate and fragile because they capture 3D scans without any physical contact, eliminating any measurement interference. The HDI Advance 3D scanner was used to capture 3D images of the pots, which contained information related to the objects’ surface measurements and textures. The information derived from the 3D images provided important clues for the GoMeasure3D team to recreate the missing pieces digitally with great detail and accuracy.
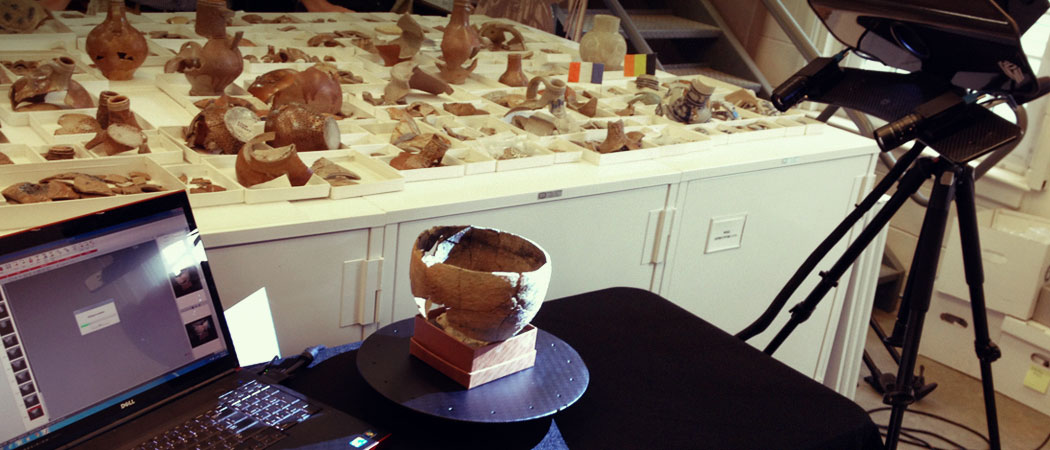
3D Modeling: Creating the Missing Pieces Digitally
Once the measurements and texture information was collected, a suite of Geomagic software was used to recreate the missing fragments. Geomagic Design X processed the scanner data for clean up and identified the broken edges where all of the missing parts need to be recreated. Once these edges were found, the preliminary shape of the pottery was reconstructed and the 3D model was transferred to Geomagic Freeform.
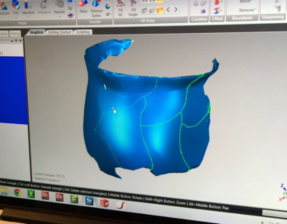
Geomagic Freeform made virtual clay modeling possible, which was ideal for this project that involved objects with organic sculptural forms. GoMeasure3D’s applications engineer modeled the shape and surface texture of the missing pottery pieces using Freeform’s touch haptic 3D stylus. The tool provided absolute control to reconstruct the fragments to be as close to what it should have been to the original pieces. During this reconstruction process, Geomagic Control was also used to ensure the authentic and reconstructed fragments fit together perfectly by comparing their measurements.
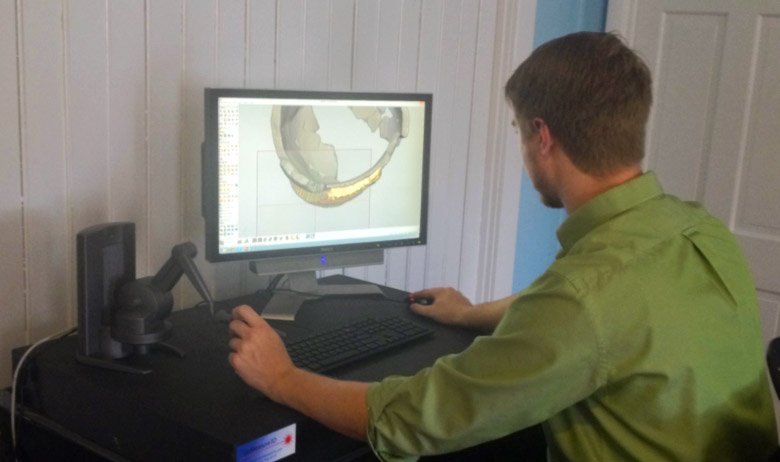
3D Printing: Digital to Physical
The GoMeasure3D team sent the completed digital files of the reconstructed fragments to the Engineering Lab at Sweet Briar College. They printed the new pieces in ABS plastic using the Dimension 3D printer. Once all the pieces were printed, they were sent to Jamestown to be assembled. They fitted perfectly with the original fragments to bring the potteries back to completeness.
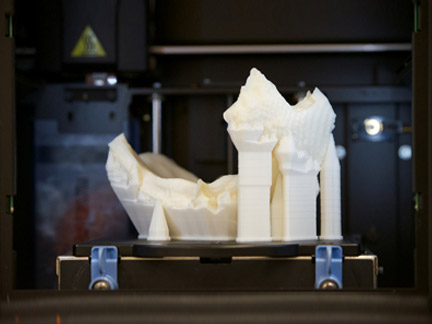
3D Technology
Processes that made this project possible
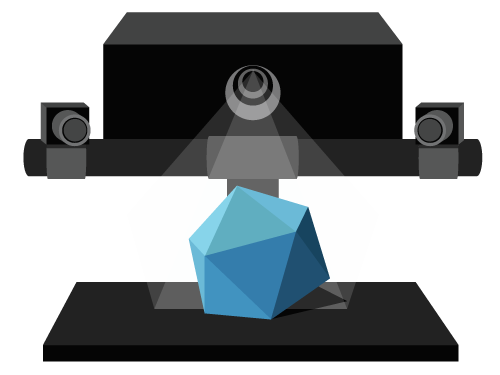
3D Scanning
Capturing 3D images of authentic pottery shards
Output
3D measurements and surface texture information
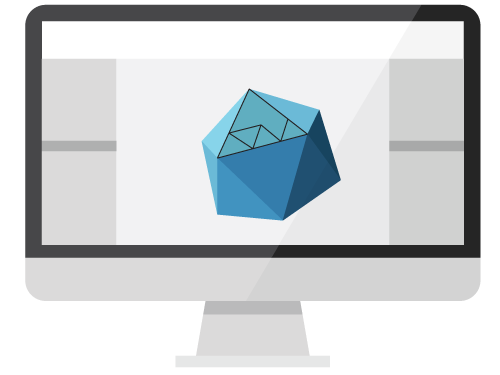
3D Modeling
Recreating missing fragments to create complete artifacts
Output
Digital files for 3D printing
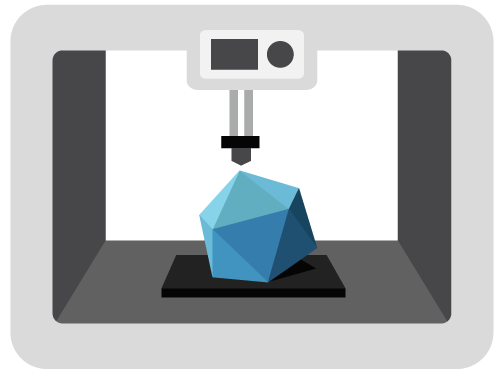
3D Printing
From digital to
physical form
Output
3D printed parts filled in to create complete pots.
Recreating the Past
The artifacts provided historical evidence that the English settlers adopted the Virginia Indian culture by adapting objects and technology into their own. One of the highlights of the exhibition was the basket pot created by Englishman Robert Cotton. He pressed clay inside a Virginia Indian thrush basket and fired the pottery in a small kiln to create the basket pot. “When he fired it, the basket burned away leaving the negative on the outside,” said David Givens, Senior Staff Archaeologist at Jamestown Rediscovery.
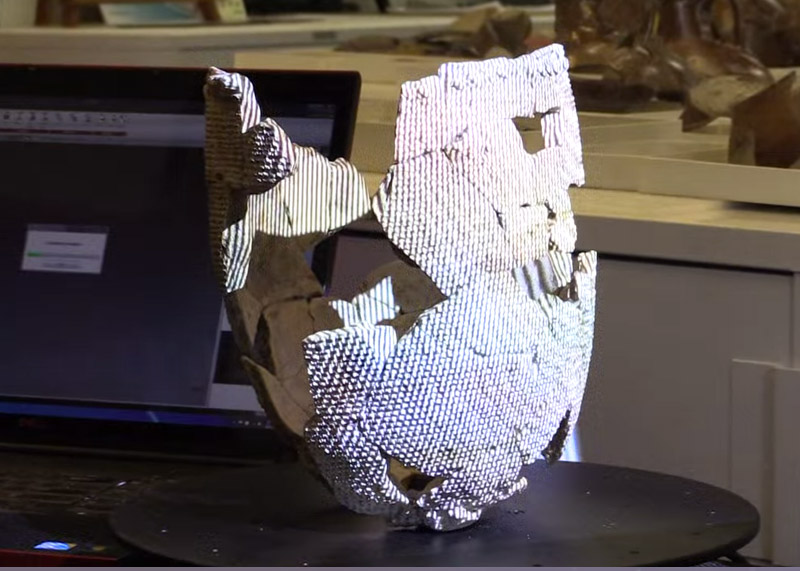
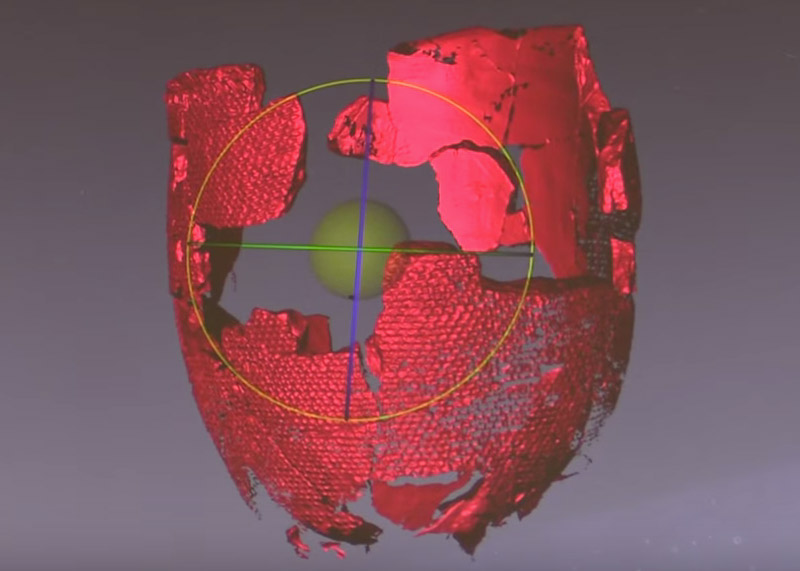
The archeology team was able to recover one-sixth of the pot in the form of fragments, with the texture of the Virginia Indian thrush basket remaining on the ceramic pot. To enhance the visualization of this particular artifact further, the 3D technology team was tasked to recreate the actual thrush basket from the impressions left of the pot. The exhibition provided the opportunity for the public to see what an actual Virginia Indian basket would have looked like for the first time.
“Through this [imaging and printing] process here, we’re going to end up creating a positive of the only Virginia Indian basket that’s ever been seen.”
David Givens Senior Staff Archaeologist Jamestown Rediscovery
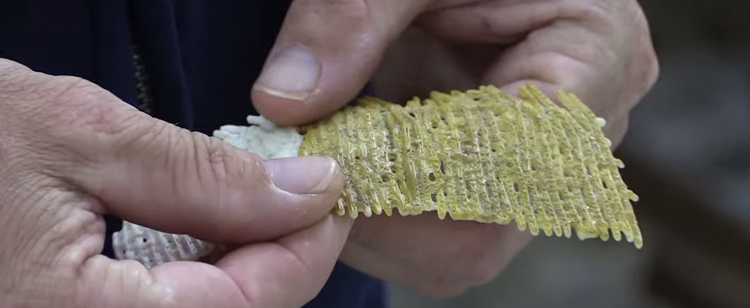
3D technology made it a possibility to recreate the missing pieces with accuracy and completeness. It provided museum visitors an enhanced experience by getting a better understanding of the American history while honoring the past.
Sources (including photos): Jamestown Rediscovery, Sweet Briar College